Suzsmokeyallan wrote:To make a cylinder puller plate its advisable to use a piece of material of at least 1/2 inch thick flat steel plate.
Then using the cylinder head as a template, mark the locations of all the holes, then drill them out and tap the ones for the cylinder pusher bolts accordingly.
Use a 10MM X1.25 pitch tap for the best results and hardened bolts of sufficient strength and length to avoid damage to the bolt and threads in the plate when under use. See if you can find bolts with concave ends so they will sit onto the crowns of the engine studs and not slip off or skew to a side of the stud.
Also, use high tensile 8MM bolts for holding the plate to the barrel and make sure they have full length threads so you obtain maximum thread grip.
If you use the regular short 8MM bolts that were in the head they will stretch and possibly rip out the threads in the barrel.
The removal process depending on the barrels tightness can be tedious and slow, plus "keeping it even" is the way to go. Always watch the distance between the base of the barrel and the upper case when lifting.
Never let it tilt from left to right as you are in effect bending the connecting rods in this situation. A tilt from back to front or left to right also adds due tightness as you are binding the already frozen fit on the case studs.
Always monitor the tension on the bolts too, sometimes during the initial lift when its stuck the hardest its best to torque them; leave them for about five minutes, then give the bolts a sharp hit to the head and try for a another shift.
You will know if its moving by the way they turn right after a hit. A little freeness in the turn usually means it lifted a micron at the initial shift and you are on your way to removal.
Sometimes one or more studs will be extremely difficult at the initial move. You can feel this by the way those bolts are resisting the lift compared to the others. A bit of heat carefully applied to the lower area around the stud has been known to help, but you have to use your discretion when doing this.
Dont forget to be generous with lube on the bolt threads and some soaking with PB blaster down the stud holes beforehand cant hurt either.
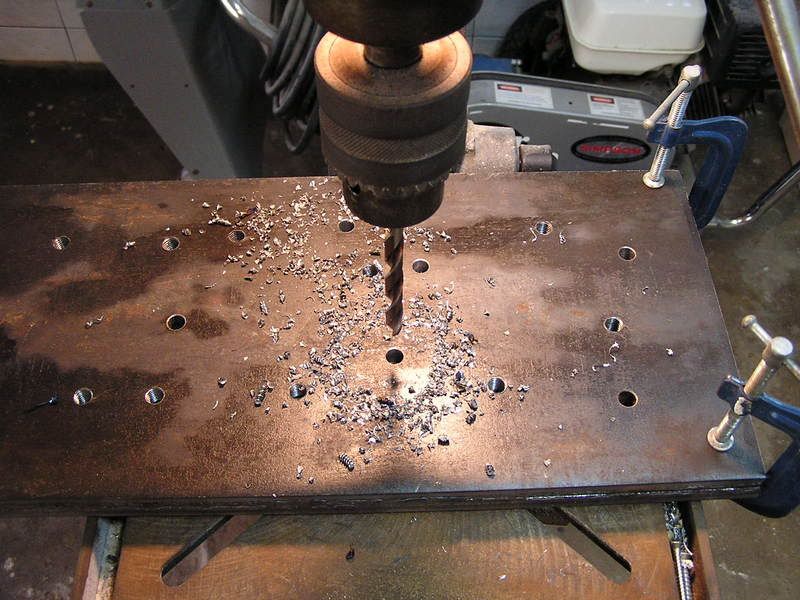
Drilling the holes into two 1/2 inch plates I've clamped together.
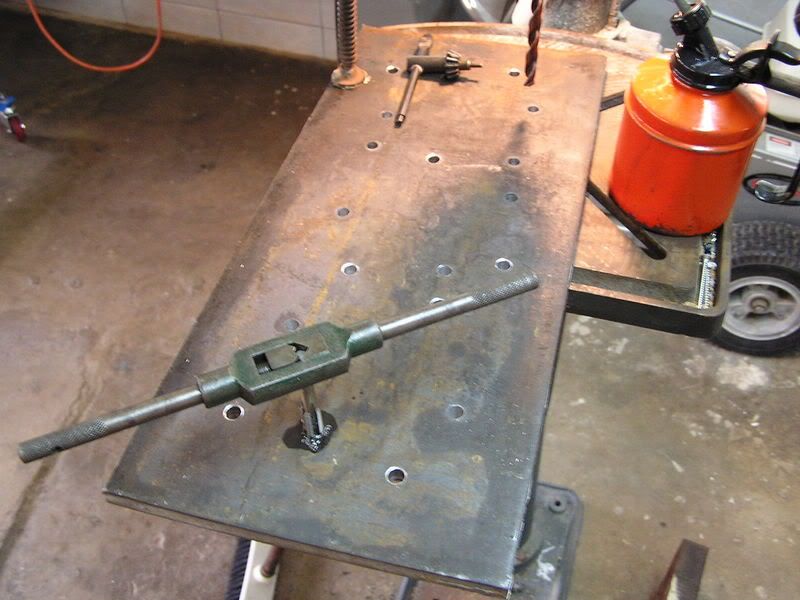
Threading the holes to 10MMx 1.25 in one of the plates at a time.
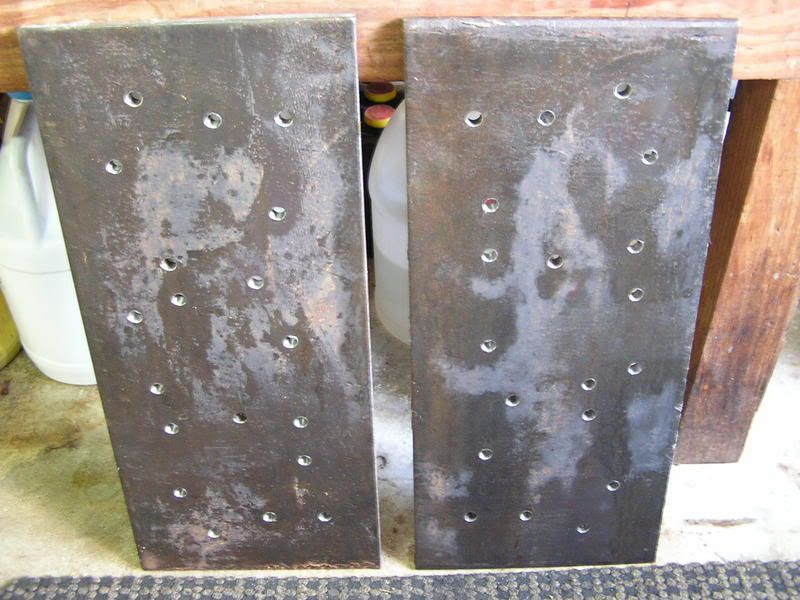
Two puller plates made up and ready for use. One was for Suzukidave and one was for myself.
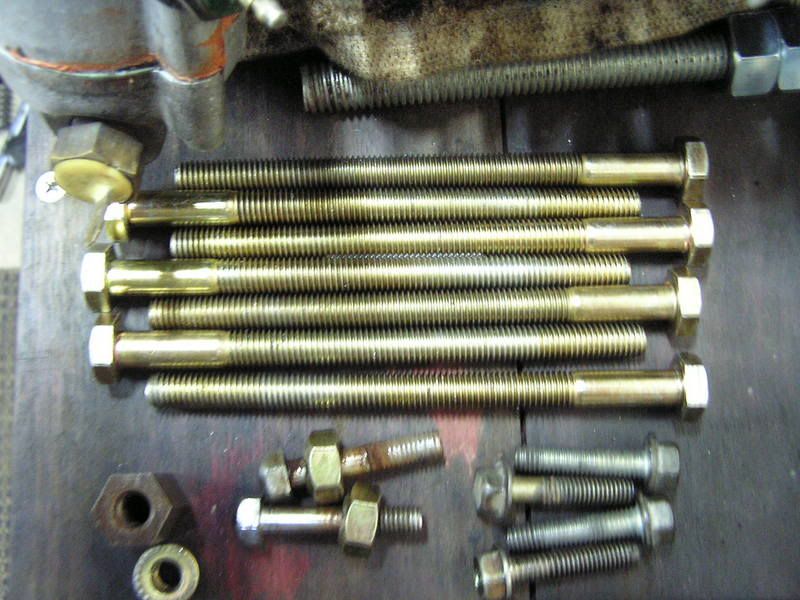
The high strength long 10MMx 1.25 bolts for pushing onto the case studs.
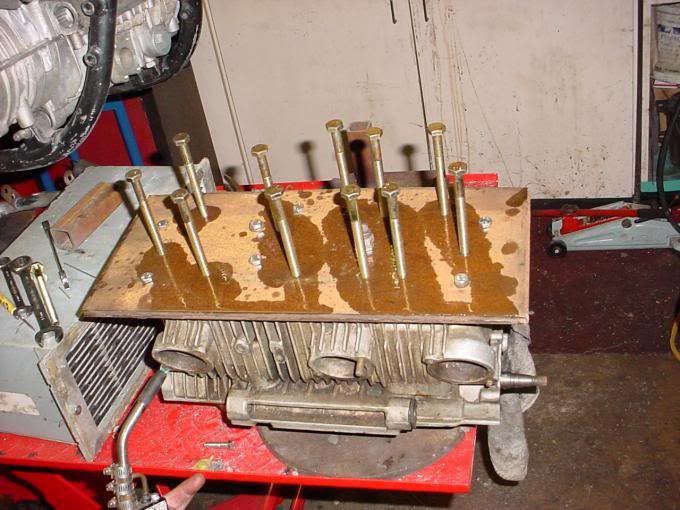
The puller plate mounted onto a barrel (photo courtesy of member Suzukidave)
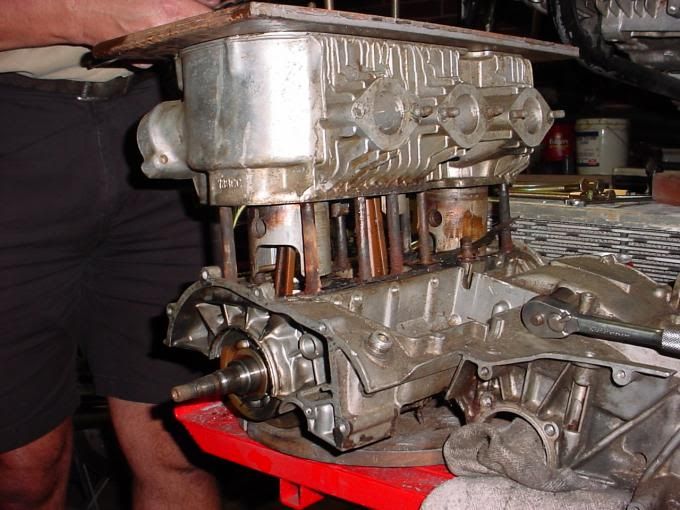
Here I am with the barrel almost lifted clear of the studs, it was still a tight fit even at this height (photo courtesy of member Suzukidave)