Page 1 of 1
All Balls question
Posted: Fri Nov 14, 2014 10:08 am
by Coyote
The last ones I installed did not have these dust shields. Though the part number was the same, this set was listed for dirt. I guess that's why the dust shields were included in the package.
Does one of these go top and bottom? Are both used or should I just omit them?
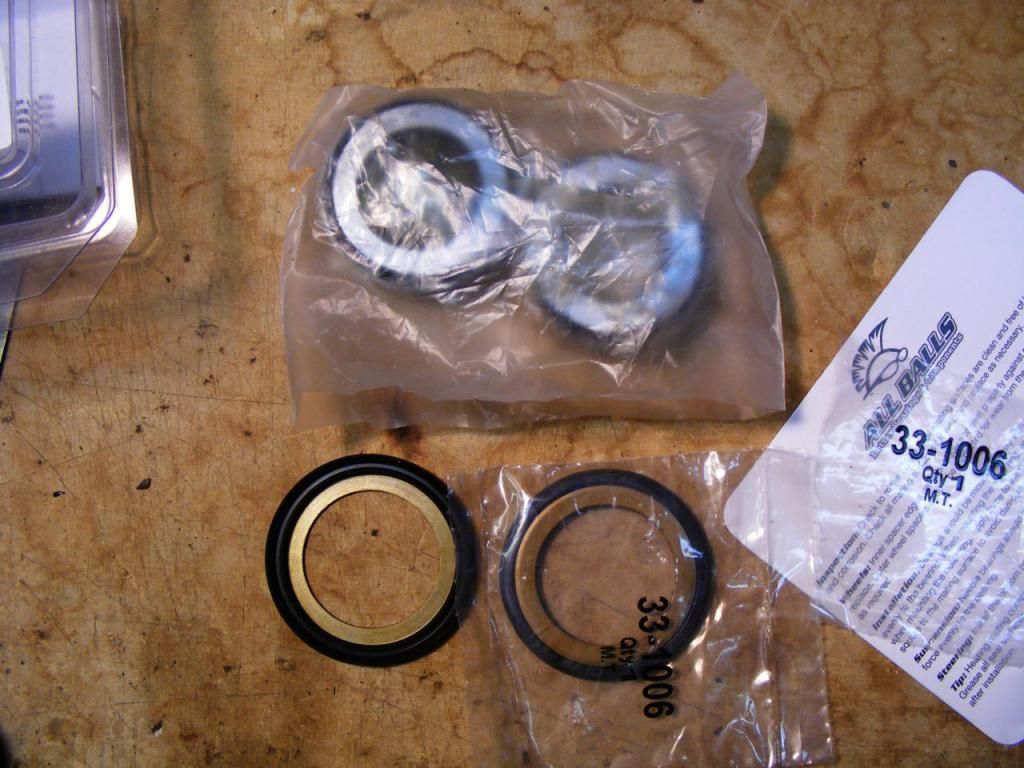
Re: All Balls question
Posted: Fri Nov 14, 2014 12:15 pm
by RING_DING
I omitted them on mine. Even then I still ended up with a gap between the headlight ears and the top triple clamp.
Re: All Balls question
Posted: Fri Nov 14, 2014 1:41 pm
by Coyote
I think I am going to use them. Assembled height will only increase .050. My headlight ears are so rusty I may end up using aftermarket brackets. It's a real shame. The stock ears have decent chrome on the outside and the tubes. The inside of the ears are super rusty.
Re: All Balls question
Posted: Fri Nov 14, 2014 3:38 pm
by yeadon_m
If these are tapered roller bearings, you can thin the steering stem a fraction using a file or dremmel tool to allow the top bearing to drop down a bit lower and close up the headlamp bracket gap. I've done this 3 times on GTs with All Balls tapered sets. They're meant to be a drop-in replacement but they're not quite that.
I also left out the seals. I did put a huge dollop of LM grease in the steering head as well as to drive grease curly fashion into the bearings!
Cheers,
Mike
Re: All Balls question
Posted: Fri Nov 14, 2014 4:38 pm
by tz375
Chris, if your headlamp ears are not in great condition, but the forks legs are fine, Check out a set of GS750/850 etc headlamp ears. They fit "inside" the fork legs and look much cleaner - IF the chrome on the legs is good.
Re: All Balls question
Posted: Fri Nov 14, 2014 9:17 pm
by bill in okc
Those ears might clean up real nice if the outside is 'nice' and they are not bent. I took mine -your description sounds the same- to a chrome shop and they look like new. It costs some but not as much as new ones and finding a good set at a reasonable price is tough.
Re: All Balls question
Posted: Fri Nov 14, 2014 9:38 pm
by Coyote
I know exactly the ones you are talking about Richard. I have a freshly refurbished pair for my GS1000. However, those forks are 37mm The chrome is good all the way up on these forks so that type would work. The left fork has some rust freckles below the lower tree - above the sliding area. Not severe but unsightly. I'd like to have another tube but singles never come up. The right tube has zero rust.
Re: All Balls question
Posted: Sat Nov 15, 2014 4:46 am
by joolstacho
yeadon_m wrote:If these are tapered roller bearings, you can thin the steering stem a fraction using a file or dremmel tool to allow the top bearing to drop down a bit lower and close up the headlamp bracket gap. I've done this 3 times on GTs with All Balls tapered sets. They're meant to be a drop-in replacement but they're not quite that.
I also left out the seals. I did put a huge dollop of LM grease in the steering head as well as to drive grease curly fashion into the bearings!
Cheers,
Mike
Okay, so I am doing this right now, and I'll throw in my findings to (hopefully) assist others who do it. Sorry if it's bit long-winded.
I needed to machine the top section of my steering stem to fit the top taper bearing inner race. The instructions that came with the AllBalls Taper Roller bearing conversion kit recommended machining the top of the steering stem (just below the bearing adjuster nut thread) down from 10mm to 16mm to the diameter of the existing machining (24.85mm in my case). The machined section is the shiny bit just below the thread that the bearing adjustor nut runs on. My stem was machined to a slightly differently measurement to the AllBalls instruction sheet. (8mm down from the threaded section as opposed to AllBalls stated 10mm). No drama... I think the key is to machine down at least 16mm below the bottom of the threaded section. I don't think it would matter if you went down further anyway. It's the diameter and alignment that's more important
The taper bearing inner race has to be able to slide up/down the stem without any play or any slop, so that the taper bearing can be adjusted so that there is virtually zero clearance and zero drag. This machining is not a dead easy job on your average 'roughie home workshop' lathe (such as my 110 year old Seneca!!!). I set it up so that the top end of the stem was chucked, and the lower end with the lower triple clamp was mounted in a live centre in the tailstock. One issue is that that the lower triple clamp is a large out of balance spinning mass quite a long way from the machining zone, that when chucked up with the live centre at the lower triple clamp end can cause a vibration that can affect the accuracy of the cut, plus it's not easy to get a perfect alignment of the top of the stem and the lower end/triple clamp. Of course with sophisticated machinery it may be a little easier, but I suspect that even with super CNC machinery, the imperfections of the (40 year old) stem assembly would make it hard to get it perfect. (Best I could manage was a radial .0015" error).
The ideal obviously is a perfect alignment of the new cut to the original machined diameter. The way I'm looking at it is this: The taper-roller bearing adaptation means that you need to get a little more machined area down the stem so that the top inner race will be able to slide down further to it's correct position when the taper roller bearing is adjusted correctly. The new race will be in a slightly lower position on the stem than the original ball race. You need a pretty accurate cut to get this right. My guess is that the 'new' cut should be -if there is any error - SLIGHTLY smaller diameter than the existing machined diameter. so the existing machined diameter will provide the correct alignment and 'fit', but the extra 'new' machining will allow the bearing inner to slide down a little more on the stem.
(Machinists please correct me if I'm wrong!) I'll let ya's know how I go when I come to assemble the thing.
I intend to use the supplied grease seals, I'll see how they go. (Doesn't seem a problem to me to pack out the headlamp mounts if needed).
Re: All Balls question
Posted: Sat Nov 15, 2014 8:12 am
by Alan H
I 'turned' the stem of my GT550 down with much pulling and tugging of lengths of emery cloth. Works fine if a little laborious.
My lathe is too small to do that, and the bottom the triple tree would make it so far out of balance when rotating, it would shake it all to bits if I extended the centre with an extended shaft and a steady on the end of the lathe bed unless it rotated very slowly!!
Re: All Balls question
Posted: Sat Nov 15, 2014 8:47 am
by Coyote
I think you have over complicated things (35 yrs machinist). It makes no difference if the new cut is blended in with the old cut nor does it matter if the new cut is smaller. Nothing touches the new cut. It's merely to get the shoulder out of the way. The bearing still only fits on the original machined area.
So the new cut can be dead nuts to the one above it, or ANY size less than the undisturbed original diameter. Wouldn't matter of it was .001 smaller or .060 smaller. And the length of the cut matters not either. You can machine the whole length of the stem if it makes you happy - stopping short of the bottom fit. You are not creating a new bearing fit. Just moving the shoulder on the stem out of the way so the bearing can pull up any slop.
All Balls could correct this situation by incorporating a larger radius on the bottom of the bearing ID. The problem though is that no 2 stems are alike. The length of the original cut must have had a wide open tolerance. Some need the shoulder moved back farther than others so they chose to just leave it alone.
Re: All Balls question
Posted: Sat Nov 15, 2014 11:11 pm
by joolstacho
Mate, thanks for the expert info. I guess it's one of those jobs a bloke needs to DO and SEE to properly get it.
I suspected a reduced diameter on the 'new' machining would be okay but didn't want to get it wrong if I'd overlooked something.
Cheers.